Business Success: How Laser Marking Devices Revolutionize Metal Fabrication
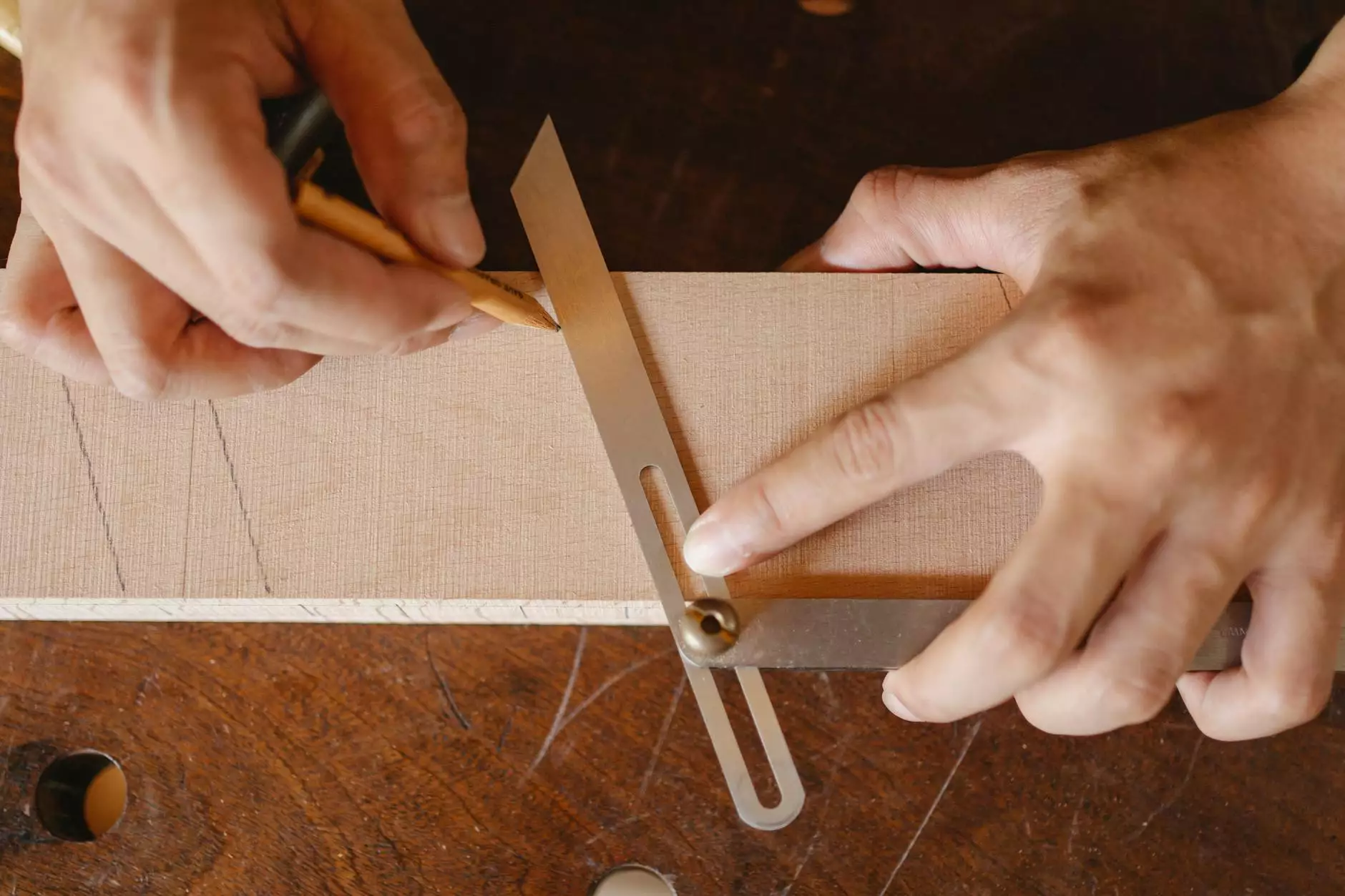
The Evolution of Metal Fabrication
As we enter the digital age, the metal fabrication industry continues to experience rapid transformations driven by cutting-edge technologies. Among these technologies, laser marking devices have emerged as a game-changer, revolutionizing the way businesses mark and engrave metal surfaces. At DPLaser.com, we are at the forefront of this innovation, offering top-of-the-line laser marking devices that provide unparalleled precision, flexibility, and efficiency in metal fabrication processes.
Unmatched Precision and Permanence
Traditional marking methods often come with limitations such as uneven marking, fading, or pre- and post-processing requirements that delay production timelines. Laser marking devices eliminate these shortcomings by harnessing the power of lasers to create accurate, permanent, and high-contrast marks on metal surfaces.
Our laser marking devices utilize advanced technologies to ensure precise and consistent results every time. With customizable settings, you can achieve intricate designs, alphanumeric codes, logos, and barcodes with ease. The laser beam's ability to concentrate intense energy in precise spots allows for microscopic marking, even on the most delicate surfaces.
Enhanced Efficiency and Time Savings
Time is a valuable resource in any business, and laser marking devices certainly unlock significant time-saving benefits. Traditional methods like chemical etching or mechanical engraving involve lengthy setup processes, while the laser marking devices offered by DPLaser.com are designed for streamlined workflow integration.
Setting up our laser marking devices is a breeze, and the intuitive user interface ensures that even novice operators can quickly adapt. This means minimal training time and maximum productivity for your business. The ability to produce consistent, high-quality marks at a rapid pace significantly reduces production cycle times, ultimately boosting your bottom line.
Wide Range of Material Application
Flexibility is paramount in metal fabrication, as businesses often work with various materials. Our laser marking devices are not limited to specific metals and can easily mark a wide range of materials, including stainless steel, aluminum, titanium, brass, copper, and more. This versatility allows you to expand your offerings without investing in multiple marking systems.
Additionally, laser marking offers a non-contact method, eliminating the risk of material damage or distortion. Regardless of the material's hardness or thickness, our devices achieve exceptional results without compromising structural integrity.
Cost-Effective and Environmentally Friendly
Implementing laser marking devices in your metal fabrication processes can provide significant cost savings in the long run. Unlike consumable-based methods like inkjet marking or stamping, laser marking devices have negligible material costs and minimal maintenance requirements. The non-contact nature of laser marking also eliminates the need for costly fixtures and tooling replacements.
Moreover, sustainability and environmental consciousness are increasingly vital considerations for businesses. Laser marking devices align with these values as they produce minimal waste, eliminate the need for chemicals, and consume significantly less energy compared to traditional methods. By adopting laser marking technology, you can reduce your ecological footprint while improving your operational efficiency.
The DPLaser.com Advantage
When it comes to laser marking devices for metal fabrication, DPLaser.com stands out as a reliable partner committed to providing cutting-edge solutions. By investing in our state-of-the-art technology, you open doors to enhanced precision, efficiency, and versatility in your business.
Experience the ease of use, unmatched quality, and exceptional results that our laser marking devices offer. Our team of experts is ready to assist you in finding the perfect solution for your specific metal fabrication needs. Visit DPLaser.com today and take a step towards revolutionizing your metal fabrication processes!